summary
It mainly introduces the centralized automatic control application of LN2000 DCS during the pyrolysis and quality improvement of pulverized coal. LN2000 DCS is reliable, safe, powerful and simple in operation and configuration. It has excellent application performance in the rotary kiln thermal disassembly system. It focuses on introducing the application of multi-coupling and multi-required materials temperature control in the rotary kiln. The program is clear, simple and clear, and the operation is stable.
Keywords: DCS rotary kiln pyrolysis kiln temperature measurement
1. Background meaning
Coal is an energy entity and an important strategic resource in my country, and the efficiency of coal resources development is related to the sustainable development of the economy. Pulverized coal pyrolysis is an effective coal quality separation technology, in which the pyrolysis product has a pulverized coke yield of about 70%, and although the energy contained in it accounts for about 80% [1] .
In recent years, new domestic coal pyrolysis processes have been continuously developed and improved, which has also provided technical support for the scale, efficiency and environmental protection of coal pyrolysis, and rotary kiln coal pyrolysis technology has emerged. The control system of the rotary kiln is the control hub in the entire pyrolysis process. How to improve and improve the electrical control of the rotary kiln directly affects the production capacity, efficiency and safety of coal pyrolysis. During the coal pyrolysis process, the rotary kiln is a large thermal equipment with a complex structure and the system has been in a dynamic change. With the influence of external ingredients, fans and other objective factors, the temperature in the kiln is constantly changing. The fluctuations in the thermal conditions in the kiln will produce low-temperature materials, high-temperature burning through the kiln skin, and the possibility of materials accumulation in the kiln are not conducive to the long-term safe operation of the kiln body and affecting the efficiency of pyrolysis capacity. In order to better control the production process and improve the pyrolysis efficiency, it is necessary to integrate the measuring instruments, signal systems, automatic execution devices and protection devices in the process through modern communication technology. The entire system must coordinate the overall situation with rotary kiln pyrolysis as the core. This requires good system reliability, good stability, rich traceability of integrated operation process, efficient and clear programming environment analysis, and good system integration, good accident response ability. According to the above situation, choosing the DCS system can better adapt to the actual requirements of the process system. The main control parts related to the control pyrolysis include six parts: feeding material, energy supply air, solid heat recovery, high-temperature dust removal, gas air induced, and reaction rotary kiln. Among them, the reaction temperature and pressure control in the rotary kiln are the soul line of the entire process operation, which is particularly important and has great control difficulties that need to be effectively solved.
After years of application, Luneng Control DCS has gained mature experience through its own practice, and has gradually deepened and expanded its functions and application scope. The LN2000 DCS has a security controller (the only one in the world is announced). The dual controller starts the IO data at the same time, the database forced information is not cleared, the SAMA configuration forced information is not cleared, and all data in the SAMA algorithm block, database, and monitoring screen are not cleared. It is a more reliable system operation, with higher fault tolerance and tolerance of accidents.
This article mainly introduces the composition and control application of coal pyrolysis system of LN2000 DCS system, and focuses on the control application of rotary kiln pyrolysis kiln material temperature.
2. DCS control system structure
From the perspective of horizontal stratification, DCS has six parts : output material control, energy supply air control, solid heat recovery control, high-temperature dust removal control, gas air induced control, and reaction rotary kiln control . Each control part has an AS station. Each AS station controls an independent control part, and communicates information with each other and becomes an organic whole. AS , OS , and ES stations are all connected together through Ethernet. They can operate independently and closely connected to each other. They can be managed centrally.
The function of feeding material control provides granular raw materials for the rotary kiln reaction device. The raw materials are transported to the upper silo above the rotary kiln reactor through belts, providing sufficient raw materials for production demand. The function of energy-transmitting air control is to provide a certain mass and quantity of thermal gases as required, providing main external energy for reactions. The solid heat recovery control mainly controls the cooling and speed reduction of the heat recovery boiler and hot materials, and ensures safety and coordination of operation. High-temperature dust removal control, control safe operation and functional logic, so that the equipment can safely filter, backblowing and switch at high temperatures. The gas air induced air control is closely connected to the quality improvement section, providing power for the gas output generated by the reaction, and closely connected to the reaction rotary kiln pressure control. The reaction rotary kiln is the core device, and all other functions of the quality improvement section are coordinated and controlled based on the temperature and pressure of the rotary kiln.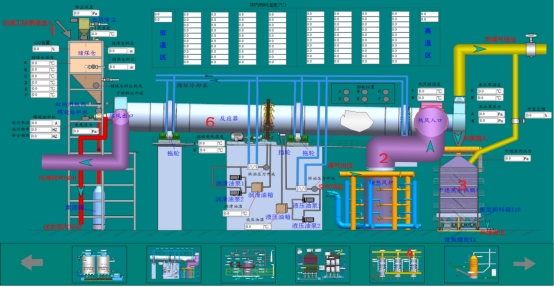
The coal pyrolysis production DCS system not only includes the contents contained in the past DCS , but also goes deep into every measurement equipment and actuator on site, and develops upward to all aspects of production governance and enterprise operations. Large coal chemical companies have very . From a vertical layered perspective, DCS has a field layer, a process management layer, and a production management layer.
1. The site layer is composed of instruments, valves, motors, etc. 2. Process management layer, namely process control station, is a computer that is centered on a high-performance microprocessor, can perform multiple process control operations, and completes analog quantity control, logic control and other functions through I/O modules, referred to as PU for short. The process control station is the most important component in the process control cabinet, and consists of the following parts: system motherboard, CPU motherboard, dual CAN interface card, power supply, housing and indicator lights, etc. The process control station is redundantly configured, real-time data communication and redundancy between stations are achieved through its built-in two Ethernet interfaces that are redundant to each other. The two CAN network controllers on the PU communicate with the I/O intelligent module in master-slave mode, have complete redundancy capabilities, and complete the management of the I/O module. Process station backup is carried out using dual network redundancy, avoiding the disadvantage of single backup through the third network or parallel cables and improving reliability. The process control station can be configured online or offline and then installed online. 3 The production management layer, that is, the central control upper-level system, completes the system operation and management of production. The main functions of the upper system include several sets of servers, several sets of operator stations, and several sets of engineer stations. In addition, it also includes photoelectric mixing industrial switches, recording printers, report printers, UPS power supplies, operating tables, etc. The operator station can read and write process data through the server, and the operator station can flexibly expand.
The field layer to the process control layer uses hard wiring to connect the instrument and electric actuators to the DCS intelligent module. The process control station and the intelligent module communicate through the field bus of the CAN protocol, also known as the I/O communication bus and the I/O communication network, adopting the dual-network redundancy method. The central control system connects the DCS process controllers of each main station through industrial Ethernet, and connects the DCS of each main station through Ethernet, communication fiber and switches to the central control room in a loop network. In the hierarchical structure of the DCS communication system, the field bus layer is used to connect to the field smart instruments, the remote bus is used to connect to the remote I/O cabinet. The control network layer is mainly used for communication between each controller and the process data server, and the operation management network layer is used for communication between the operator station, the engineer station and the process data server.
3. Control system function implementation
The DCS control system functions are mainly implemented by a series of software, which are integrated in the DCS general development environment, including: system management, system database configuration, SAMA graph configuration, graphical interface configuration, monitoring screen operation, trend curve, alarm management, historical data recording, system self-diagnosis, statistical reports, and time list. SAMA graph configuration: Based on algorithm blocks, through graphical configuration, the analog control function and logic control function configuration and related modifications of the process control station in the system are completed, and the online debugging function is also provided. The program logic is mainly used to perform the running program logic through SAMA diagram. Self-diagnosis: Self-diagnosis software is used to monitor all states in the entire DCS system from the upper operator station, engineer station to the lower process station, CAN network, module, and data channel. Provides sufficient information for users to understand the operating status of the DCS system. Event list: This software is generally run in a history station, including two parts: operation record report and SOE event report. The operation record includes operation records of all operators, and the SOE record resolution is 1ms.
In the project, define the scale of AS, OS, and ES sites, and correspond to the functional control end, and compile and configure the AS and OS through ES. The AS is loaded with the corresponding process logic of the entire control function area, and the dual PUs operate in a redundant and synchronous manner. The OS provides a human-computer interface input and output interface. The corresponding OS station mainly provides the corresponding stage control process status screen. ES arranges the number of programs based on the actual development and maintenance scale and personnel, and does a good job in program configuration development and maintenance. The project is equipped with a control station and IO module as shown in Table 1:
Table 1 Controller and module configuration table
Serial number | name | Specification | unit | quantity |
1 | Process Control Station ( LN-PU)
| Each set includes: | tower | 18 |
CPU motherboard, dual CAN interface, dual 100M Ethernet |
Power supply (220VAC, 0.5A) |
256M electronic disk (DOM), 128M memory |
2 | I/O module | LN-01B 8-channel isolated analog input module | piece | 136 |
LN-02B 8-channel isolated thermocouple input module | piece | 58 |
LN-03B 8-channel isolated thermal resistance input module | piece | 43 |
LN-05B 4-channel isolated analog output module | piece | 101 |
LN-06B 12-channel isolated digital input module | piece | 192 |
LN-07B 16-channel isolated digital output module | piece | 135 |
LN-COM Isolated Communication Module | piece | 17 |
During normal operation of the reaction rotary kiln, ensuring the stability of the material temperature in the rotary kiln is the basic prerequisite and the most important control parameter for ensuring production stability. During stable operation, the higher the temperature of the heating flue gas, the greater the gas volume, the higher the material temperature in the rotary kiln. The temperature measurement in the rotary kiln is used to measure the kiln temperature specially designed wireless transmission temperature measurement instrument developed by Zhongjuenghuan Research Institute. The temperature measurement measures the material temperature, heat exchange surface temperature, and heat-carrying gas temperature. The temperature measuring point instrument of each rotary kiln works independently. When there is a single failure, it will not affect the global measurement data, and the control basis is still reliable. Each instrument measuring point on the kiln is powered independently (power can last for 3-5 years according to the communication distance). The measurement data is transmitted to the kiln receiving terminal in wireless form. The kiln wireless terminal can display the kiln temperature measurement data on the kiln on the spot, and is connected to the DCS system through the Modbus protocol and connected to the DCS system. One kiln receiving terminal can communicate with the 90 kiln temperature measurement point instruments at the same time. The heating method of materials in the kiln is to transfer heat to the material through high-temperature gas. When the material temperature in the kiln is stable, it can meet the temperature of the key reaction sections in the kiln by adjusting the amount of hot gas and inputting hot gas temperature to ensure high quality of the reaction.
During normal operation, the feeding material part converts frequency to control the belt feeding speed to ensure that the material seal and storage of the feeding silo are in the highest position. The energy-sending air part adjusts the load by itself, controls the air ratio to ensure oxygen content, and is mainly responsible for the combustion part. At the same time, the reflux low-temperature gas is added before the air supply is supplied to the rotary kiln, and the temperature of the heating energy gas is controlled and the temperature of the heating energy gas is constant. The control part controls the heat load at any time according to the temperature of the rotary kiln material. The two key points in the solid heat recovery control are the boiler's three-flush water replenishment control and the material level of high-temperature solid material. If the high-temperature solid material level is too high or too low, it will cause equipment damage and parking accidents, ensuring that the boiler does not dry, the solid material of the pot does not jam up or be exposed. The entire process control is relatively independent, and the overall operation follows the control of the rotary kiln body. High-temperature dust removal control is mainly safety, rotation training and backblowing, regular high ash discharge, regeneration procedures, etc. The temperature must be kept stable, which is a prerequisite for the operation of left and right rotary kilns.
The gas pressure in the rotary kiln is generated by the gas produced by its own materials. During normal production, the gas induced air speed is controlled to ensure that the zero pressure in the kiln is near. Among them, the temperature distribution control of materials in the kiln is typically different from ordinary control. The control target has many input points and the output control amount is small. The priority of the control target composition changes with time, conditions and other conditions. Only fuzzy control multi-channel PID based on the expert system can be combined. By imitating human response methods, traditional computer control methods are combined to operate and control each situation in a mathematical independent way, and at the same time, the control effect is recorded and analyzed and self-corrected slowly and self-tuned.
The LN2000 comes with its own neuron algorithm, enhanced PID , device module driver, etc., which fully meets the control needs of this process. It can easily implement configuration in complex control. At the same time, data can be exchanged with expert tuning and analysis software at any time through OPC . The application of LN2000 safety controller makes the process of accidental power outage control process uninterrupted, and the program will not be run back to zero, ensuring that the process of operation is safe.
4. Summary
In the practical application of rotary kiln pyrolysis, Luneng control LN2000DCS is simple and convenient, smoothly run, reliable use, friendly interface, and integrated full operation history without blind spots. Luneng Control DCS has a modular design, powerful functions and is close to user needs; the platform is open and application services are professional, easy to use; it is more convenient to use and maintain and better service; LN2000 DCS can reduce people and increase efficiency, and the use of DCS to form a system will enable the factory to achieve the whole factory integration. The dual controller starts the IO data at the same time, the database forced information is not cleared, the SAMA configuration forced information is not cleared, and all data in the SAMA algorithm block, database and monitoring screen are not cleared, making the system more reliable operation, with higher fault tolerance and accident tolerance, and is suitable for rotating kiln pyrolysis technology.
References:
Comprehensive utilization of coke powder of pulverized coal pyrolytic products such as Li Xin, Zhang Shengjun, Xu Jie, Zheng Hua'an [J] Coal combustion 2013.19 ( 05 ) : 74-76
Zhen Ming ; Research on the pyrolysis process of coal of four different degrees of metamorphism [D]; Inner Mongolia University of Technology; 2015
Guo Xueliang . A brief discussion on the application of DCS system in coal chemical enterprises [J]. Management Tips 2013, 5.